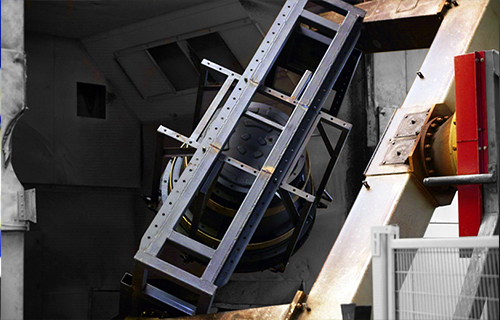
El rotomoldeo es un proceso de fabricación que ha ganado protagonismo en los últimos años por su capacidad para producir piezas plásticas huecas, ligeras, altamente resistentes, sin uniones y con acabados homogéneos. A través del calentamiento y rotación de un molde cargado con resina plástica, se consigue que el material recubra de forma uniforme las paredes internas del molde. Esto permite fabricar desde depósitos de gran volumen hasta componentes técnicos con formas complejas, todo ello con una inversión más baja en utillajes respecto a otros métodos.
Ahora bien, para que todo esto sea posible, hay un elemento imprescindible: la matriz. Las matrices para rotomoldeo no solo definen la forma de la pieza, sino también su resistencia, acabado y uniformidad. Son, en definitiva, el corazón técnico del proceso. Por eso, conocer cómo se diseñan, con qué materiales se fabrican y cómo mantenerlas en condiciones óptimas es clave para garantizar una producción eficiente, precisa y duradera. ¡Sigue leyendo para conocer todos los detalles
¿Qué son las matrices para rotomoldeo?
Las matrices para rotomoldeo son moldes diseñados específicamente para contener la resina plástica que, al ser calentada y girada en varios ejes, se adhiere a sus paredes formando la pieza final.
Estas matrices pueden ser de una sola cavidad o multicavidad, dependiendo del volumen de producción y la complejidad del diseño. Mientras que una matriz de una sola cavidad se utiliza para fabricar piezas grandes o únicas, las matrices multicavidad permiten producir varias unidades simultáneamente, optimizando los tiempos de ciclo y reduciendo costes.
Su uso se extiende a sectores muy diversos: desde la fabricación de tanques para almacenamiento de agua para la industria del transporte y otros elementos en la agricultura, hasta productos de diseño como mobiliario urbano o luminarias decorativas.
Diseño de matrices para rotomoldeo
Un diseño eficaz no solo influye en la calidad de las piezas finales, sino que también facilita el mantenimiento de la matriz y reduce el desgaste prematuro. Es por ello que, en el proceso, se deben tener en cuenta múltiples factores técnicos como:
- Materiales utilizados: Según la aplicación y volumen de producción.
- Tolerancias: La precisión en las medidas es esencial para lograr piezas consistentes.
- Geometría: Las formas complejas requieren matrices segmentadas o con insertos móviles.
- Capacidad de producción: No es lo mismo diseñar para producción en masa que para series cortas o prototipos.
Eso sí, gracias a la flexibilidad del rotomoldeo, las matrices se pueden adaptar fácilmente a distintos diseños sin incurrir en los altos costes que presentan otros métodos de moldeo.
Materiales utilizados en la fabricación de matrices
Antes de elegir el material con el que se va a fabricar una matriz, es fundamental entender qué se espera de ella. Y es que una buena matriz para rotomoldeo debe cumplir una serie de requisitos técnicos que garanticen su rendimiento a lo largo del tiempo y en diferentes condiciones de trabajo.
- Resistencia al desgaste, especialmente cuando se producen series largas y se abren y cierran cientos o miles de veces.
- Buena conductividad térmica, para asegurar un calentamiento uniforme del molde y un enfriamiento eficiente que no comprometa la calidad del producto.
- Resistencia a la corrosión, en especial cuando se trabaja en ambientes húmedos o con materiales aditivados.
- Estabilidad dimensional para que las piezas obtenidas mantengan sus medidas incluso tras muchos ciclos.
- Facilidad de mecanizado y reparación, clave cuando se requiere modificar o ajustar el molde en fases de prototipado o series cortas.
Con estas exigencias técnicas sobre la mesa, la elección del material se convierte en un aspecto estratégico que no solo influye en la vida útil de la matriz, sino también en los costes de producción, el tiempo de ciclo y la capacidad de adaptación a diferentes diseños.
Los dos materiales más usados son:
- Aluminio: Apreciado por su ligereza, buena conductividad térmica y facilidad de mecanizado. Es ideal para matrices de geometría compleja, proyectos con cambios frecuentes de diseño o series cortas y medianas.
- Acero: Destaca por su resistencia estructural y mayor durabilidad, siendo la mejor opción para producciones largas o condiciones exigentes donde el molde debe soportar un uso intensivo.
También existen aleaciones especiales, tanto de aluminio como de acero, que combinan propiedades mecánicas y térmicas mejoradas para responder a requisitos más específicos. En algunos casos, se emplean moldes híbridos, que integran componentes metálicos con insertos en materiales compuestos o polímeros técnicos, lo que permite reducir peso, facilitar reparaciones o personalizar zonas concretas del molde.
Aunque menos frecuentes, se pueden fabricar matrices en silicona o resinas epoxi, principalmente en etapas de prototipado o para series muy cortas. Estas permiten reproducir detalles finos del diseño con gran fidelidad, aunque su durabilidad es limitada y no soportan temperaturas tan elevadas como los metales.
Desafíos en el diseño y fabricación de matrices
Fabricar matrices de calidad conlleva superar ciertos retos técnicos, especialmente en lo relativo a:
- Desgaste prematuro: Una mala selección de materiales o un mantenimiento deficiente pueden reducir drásticamente la vida útil de la matriz.
- Distorsiones térmicas: Un diseño incorrecto puede provocar que la matriz se deforme con el uso.
- Control de la temperatura: Es vital que la matriz se caliente y enfríe de forma uniforme para asegurar una pieza final sin defectos.
También te puede interesar las claves para alargar la vida útil de tus productos por rotomoldeo.
La buena noticia es que la innovación tecnológica está ayudando a resolver estos problemas. Gracias a herramientas como el diseño CAD/CAM, simulación térmica, y fabricación asistida por ordenador (FAO), hoy es posible predecir y corregir errores antes de fabricar la matriz.
Un ejemplo práctico es el desarrollo de matrices con canales internos para la circulación de aire caliente, que mejora el control térmico durante el proceso de rotomoldeo y evita defectos en el acabado superficial de la pieza.
Tendencias futuras en el diseño y fabricación de matrices
El futuro de las matrices para rotomoldeo está marcado por la sostenibilidad y la innovación en materiales. Algunas tendencias destacadas son:
- Materiales más ligeros y resistentes: Las nuevas aleaciones permiten crear matrices que mantienen la rigidez estructural con menor peso, reduciendo el esfuerzo sobre las máquinas rotativas.
- Uso de compuestos y tecnologías híbridas: Combinaciones de metal y polímeros técnicos que mejoran la conductividad y reducen el peso sin sacrificar la durabilidad.
- Fabricación aditiva (impresión 3D): Ideal para prototipos de matrices o insertos personalizados.
- Procesos más ecológicos: Desde el diseño hasta la producción, la industria avanza hacia una fabricación más responsable. En este contexto, el uso de plásticos reciclados tiene un rol central.
Estas innovaciones no solo responden a demandas técnicas, sino también a una creciente conciencia medioambiental y la necesidad de reducir la huella de carbono del sector industrial.
Mantenimiento y durabilidad de las matrices
Un aspecto crucial para maximizar el rendimiento de las matrices para rotomoldeo es su mantenimiento. Un programa de mantenimiento adecuado debe incluir:
- Limpieza regular tras cada ciclo de producción.
- Inspección de desgastes o grietas.
- Lubricación de bisagras y cierres.
- Control de temperatura y alineación de piezas móviles.
Invertir en un buen mantenimiento no solo prolonga la vida útil de la matriz, sino que garantiza una producción sin interrupciones ni defectos. Esto se traduce directamente en ahorro de costes y mejora de la resistencia y durabilidad de las piezas rotomoldeadas.
En resumen, las matrices para rotomoldeo son herramientas esenciales para garantizar productos plásticos de alta calidad. Su diseño, materiales y mantenimiento influyen directamente en la eficiencia, sostenibilidad y rentabilidad del proceso de producción.
En un mercado cada vez más competitivo, contar con matrices optimizadas y bien mantenidas no solo representa una ventaja técnica, sino también una apuesta estratégica por la innovación, la durabilidad y el respeto medioambiental. Desde matrices multicavidad hasta tecnologías de fabricación híbridas, la evolución de estos componentes sigue marcando el ritmo del rotomoldeo moderno. Y en este camino, la inversión en calidad y diseño seguirá siendo clave para quienes desean diferenciarse en la industria.